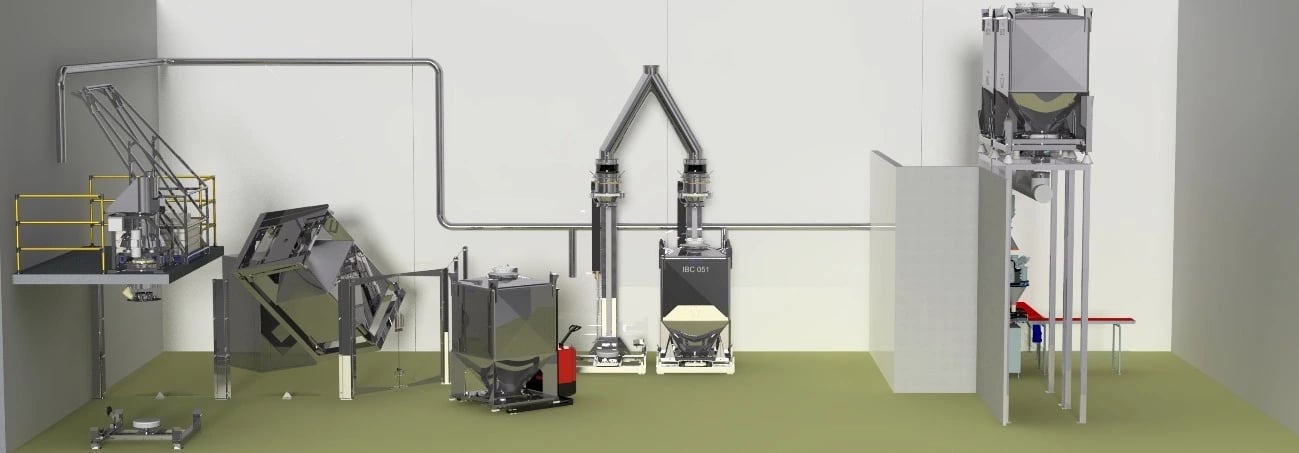
INDUSTRIES
Processing and mixing equipment infant nutrition
We help manufacturers of infant formula and baby food achieve agile and flexible manufacturing systems in a highly regulated industry.
YOUR CHALLENGES
Mixing challenges for infant nutrition manufacturers
When producing sensitive products such as Infant Formula and Nutrition and other high containment products, installing the right processing equipment from the outset is vital. Achieving the highest food safety levels is always the priority.
Bacteriological contamination is a constant risk when processing nutrition powders.
Milk powder is notoriously difficult to handle, being sticky and poor flowing.
Ensuring that the micro-ingredient fortifiers are well distributed & mixed can also be a challenge.
HOW WE CAN HELP
Improve infant nutrition manufacturers productivity
Matcon IBC Systems are designed to provide flexibility so that production processes can easily manage varying order sizes and large recipe portfolios whilst maintaining tight hygiene standards.
Central to our IBC technology is the Cone Valve, offering automatic and controlled discharge of virtually any powder type. Cohesive materials are stimulated to flow, whilst free-flowing powders are controlled. Our Cone Valve has continually proven to overcome the traditional powder handling issues of bridging, rat-holing, segregation and degradation.
Infant formula contains a number of vitamins and minerals which are added in small quantities. Blend homogeneity is critical to maintain product quality and the Matcon IBC Blender is industry proven in providing low CV values.
Our IBCs are designed for easy cleaning of the internal surfaces with no exposure to cross-contamination. Using only air removes the risk of waterborne bacterial growth, particularly useful in dairy and infant nutrition powder applications.
Our scalable modular system that allows for process flexibility as you innovate and grow your product portfolios in the future is a very good investment choice.
OUR EXPERIENCE
Comply with strict safety, hygiene and nutritional standards
Matcon has years of experience from working within the pharmaceutical sector therefore we understand the importance of complying with strict safety, hygiene and nutritional regulatory standards.
Our customers include national and international infant formula and baby food manufacturers from around the globe.
We design efficient and flexible IBC systems to allow our customers to grow by increasing production output and enabling them to widen their product portfolio without the risk of cross-contamination across batches.
Our IBCs are hygienically designed to the highest specifications, meeting with EHEDG, GMP and FDA standards.
OUR APPROACH
Working with infant nutrition manufacturers
From batch consistency to homogeneity, segregation during transfers to validation of equipment washing and drying, from consistent batch ingredients to maintaining hygiene levels, the Matcon team are here to help solve your processing challenges.
Fully contained at all times, our system is dust-free and reduces the space required for clean-room or safe zone status.
Matcon use ADUs (Auto Docking Units) at every IBC filling position to ensure powders are never exposed to the atmosphere. Once powders are inside the IBC, they remain sealed and contained until the blended product is packed.
Near-Infrared (NIR) Spectroscopy technology is used to prove blend homogeneity. This reduces blending time, prevents over-mixing and eradicates the need for invasive sampling.
Our stainless steel IBCs are hygienically designed for ease of cleaning and coupled with our air wash capability, reduces the likelihood of any waterborne bacteriological infection.
Mass flow created by the Matcon Cone Valve significantly reduces the chances of segregation during transfer to packing, ensuring you get a perfectly homogenous mix right to the end of the batch, vital when producing top-quality infant nutrition products.
SYSTEM MODULES
Powder Handling Systems for Infant Nutrition
This simple system is all you need to get started the right way. By decoupling the processing steps we enable companies to achieve a flexible manufacturing system.
The Matcon system is based on using Intermediate Bulk Containers (IBCs) to transport powders between manufacturing steps and as a blending vessel. Because everything is contained within the IBC, there is no clean-down of the blender between recipe changes, which gives you the ultimate flexibility of operation.
LEARN MORE
Resources and Information
Equipment guidance and useful information for manufacturers of infant nutrition.
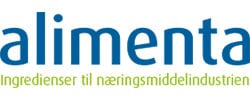
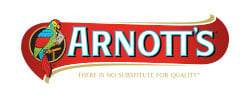
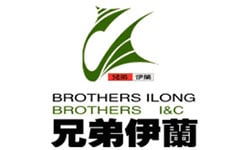
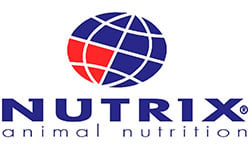
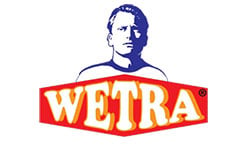
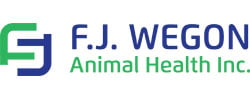

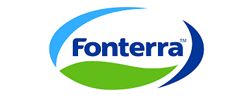
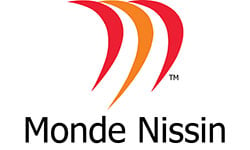
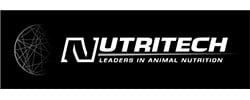
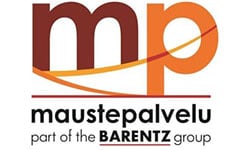
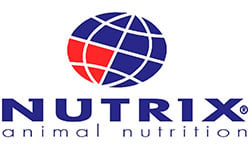