Powder Bridging
How can you avoid powder briding and prevent poor powder flow?
Is your expensive product getting stuck in your silo, bin or hopper? Do you have to exert rigorous external vibration to release the powder?
The reason that your powders are not freely discharging could be due to powder bridging (arching).
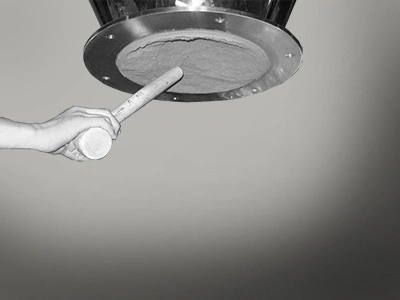
Why Do I Have Poor Powder Flow?
Poor flow can be costly and cause further issues downstream.
The variety of different powders used in product recipes means that any batch will have a range of particle characteristics with differences in size, shape or density.
The flow properties of the material is affected by the collective forces acting on the individual particles. Bridging of powders occurs when materials interlock or bond together to build an arch above the outlet of a container – which could be a silo, IBC, hopper or mixer vessel.
Cohesive strength and the internal friction of the individual particles will determine the potency of the arch itself. When this occurs the arch holds the rest of the bin’s contents preventing discharge of the remaining powder.
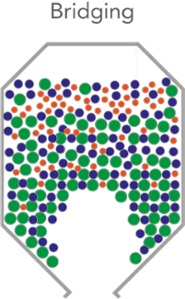
What are the Common Causes of Powder Bridges?
Obstructions formed in your containers can be the result of a number of factors.
Butterfly or slide valve bins are prone to problems with arching and bridging. This is due to the contents immediately above the outlet being able to easily flow outwards once the valve is opened. If any of the material above this has interlocked or bonded together, this will result in a bridge forming above the outlet. As there is nothing within the bin to break this arch and make it flow, your product will get stuck.
To resolve this issue, operators will often need to stop the line and intervene by hammering the outside of the bin. This action raises several issues, namely damage to the bin in the long term. Also the hammering itself can cause further segregation of the mix. This common powder handling problem will affect production efficiencies and product quality, increasing costs whilst reducing quality.
How to Overcome Bridging
If your powders stop flowing during discharge it could be due to bridging.
The Cone Valve technology within each of the Matcon IBCs overcomes powder bridging due to both the lifting action of the cone and its integral vibration during lift.
The raising and lowering of the Cone Valve within the IBC, combined with the internal vibration disturbs & agitates the full cross section of the powder in the container reducing the risk of a uniform powder bridge.
Because there is a constant feed of product, without any risk of hold-up, it is possible to automate the discharge process and supply a regular feed of material to the downstream processes.
CONTACT US
Looking to Resolve Powder Bridging?
If you're having issues with powder flow in your manufacturing process, complete the form below and one of our powder handling experts will be in touch to help you solve the issue.
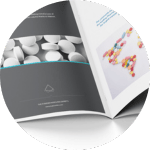
Case Studies
Read on to discover how we help companies around the world create flexible, agile manufacturing plants.
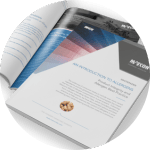
White Papers
Understand more about how to get the best from your powder handling site with our resources.
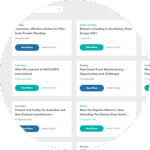
Blog
Read more about powder handling solutions, technical advice and industry insights from the experts.