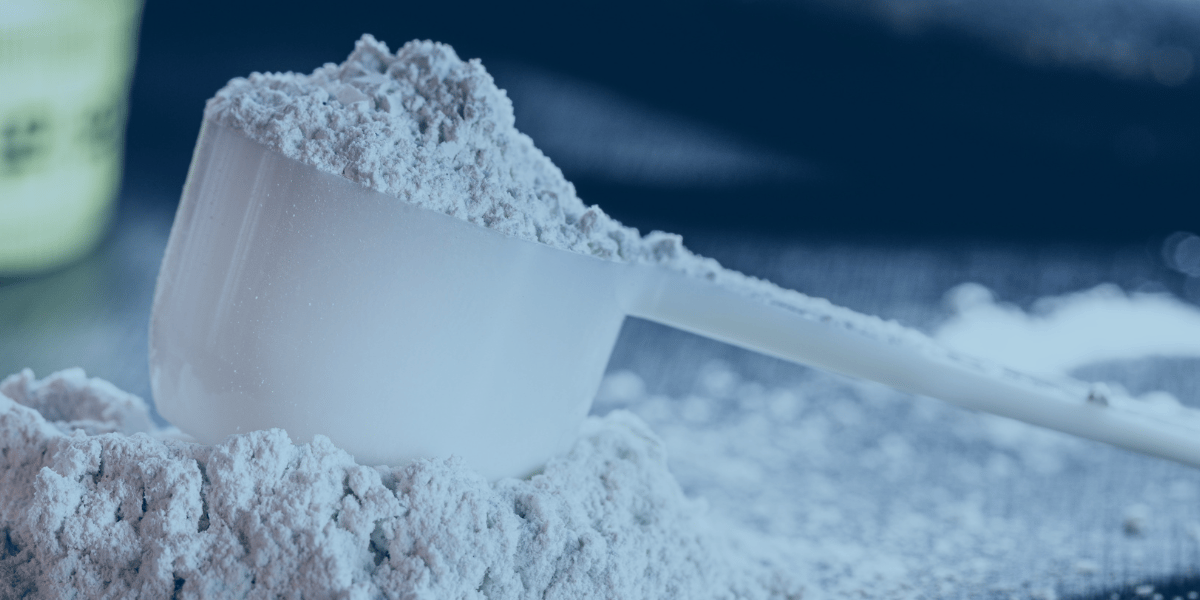
Sports Nutrition Powder and Fitness Supplement Manufacturing
Manufacture high-quality sports, health and well-being supplements using efficient, safe, proven powder-handling equipment. From recipe formulation to powder mixing and packaging, Matcon has you covered.
18 Min Read Time
Powder Handling Systems for Sports Nutrition Production
As product portfolios expand and recipes change, handling sticky powders and preventing allergen contamination become increasingly challenging, often resulting in longer cleaning times.
Matcon systems enhance production flow by using separate modules for each process step, allowing simultaneous operations. The unique Cone Valve in each Matcon IBC ensures accurate 'mass flow' material discharge without mix segregation. 'In-bin blending' minimises downtime from cleaning and mitigates cross-contamination risks.
Matcon IBC systems are suitable for sports nutrition manufacturers of all sizes, serving start-ups and market leaders across the globe.
1.1 BENEFITS OF IBCS
Benefits of IBC Systems for Sports Nutrition
Matcon's powder handling equipment enables manufacturers of sports nutrition supplements to stay ahead in a competitive market.
Your Challenges
- Expanding portfolios result in many changeovers which significantly impact on available production time.
- Sports and nutraceutical powders are notoriously difficult to handle being sticky and poor flowing. New plant proteins are likely to be even more so.
- Increasingly, recipes contain allergens which means even more time spent in thorough clean-downs.
How We Can Help
- A system designed to optimise production flow is what we do. All process steps occur simultaneously for maximum efficiency.
- The unique Cone Valve in each IBC protects the blend and provides assured discharge, even on sticky mixes.
- In-bin blending reduces downtime for changeovers and removes the risk of cross-contamination for sports nutrition manufacturers.
Prevent cross-contamination
Trace
allergens
Prevent
bridging
Fast recipe changeover
Prevent mix segregation
Reduce cleaning times
Why Matcon for Sports Nutrition Manufacturing
Flexible Scalability Enabling You to Adapt to Your Market
As the sports nutrition industry continues to grow, the opportunity for manufacturers increases.
Scaling up your production can be difficult, especially when you only have limited factory space and investment. When you're looking to scale up, IBCs give you an advantage, ensuring that you increase flexibility and adapt as consumer demand and preferences change.
Whatever the product, it is always worth having expert advice from an experienced solutions provider for the sports nutrition industry.
Increase Production Capacity and Efficiency Without Compromising on Product Quality
The sports nutrition industry is now big business with everyone from serious athletes to health conscious shoppers regularly purchasing a wide range of products.
With such a wide range of customers, requirements and demands a flexible solution is a must to keep you ahead in a competitive market place.
Matcon provides a range of innovative solutions to meet such demands, enabling sports nutrition manufacturers to quickly and effectively switch between the production of flavours and batch sizes without the risk of contamination.
Effective Allergen Handling for Sports Nutrition
Contamination from potentially harmful allergens can lead to serious problems for customers.
As product integrity becomes more of a focus for sports nutrition, manufacturers must know exactly what is going into their products and what will end up in the hands of the consumer.
With wheat-free, dairy free and vegan diets also becoming leading consumer trends, manufactures in the health and well-being market must deliver on quality but without sacrificing production efficiency.
Discover how IBCs can support manufacturers looking to establish clean, cost-effective production lines and meet the demand of consumers without sacrificing return on investment.
Reduce the Time You Have to Spend Cleaning
Less time spent cleaning means more time can be allocated for production.
All sports nutrition manufacturers need to change over recipes, which ultimately means time must be spent cleaning. When using a fixed line, cleaning usually results in downtime where you are not producing product.
We estimate that some manufacturers using fixed mixers (ribbon blenders or paddle blenders) could lose at least 20% of the shift to cleaning time. As the blender must be fully cleaned and dried before changing recipes your whole production process must be halted.
Read our guide to increase efficiency and ensure your resource time is spent producing high volumes of quality products and not cleaning and assembling a blender.
1.3 IBC vs RIBBON BLENDER
IBC Blenders vs Traditional Ribbon and Paddle Blenders
View our system comparison video to see how a Matcon approach delivers a higher ROI than a traditional fixed-line mixer system.
In the competitive sports nutrition industry, you must have a manufacturing system that provides you with the ability to manufacture multiple batches - efficiently and safely. If you have the ability to change recipes, clean down and run other batches simultaneously, then you will not only keep pace with a demanding marketplace but remain one step ahead of your competition.
Getting Started in Sports Nutrition Manufacturing
As the health and well-being industry grows at a rapid rate, new providers are looking to enter the market.
With market growth comes increased competition and wider product variety, as sports nutrition and dietary supplement manufacturers look to secure market share. Those manufacturers looking to scale up production need the correct manufacturing equipment that will help them manufacture their products in a cost-effective way. Whether you are a start-up or established provider, you can benefit from lean manufacturing.
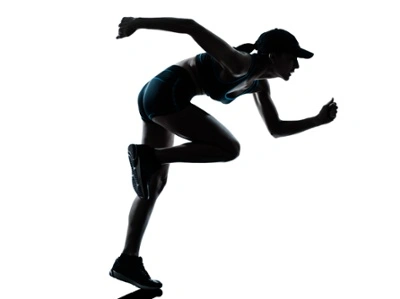
2.1 WHAT TO CONSIDER
Key Considerations for Scaling Sports Nutrition Manufacturing
What do you need to consider when starting to manufacture sports nutrition products & nutritional supplements?
As demand for sports nutrition products grows, small manufacturers face specific challenges when considering expansion. It is important to assess the direction of your business, such as whether you plan to target mass markets or focus on specialist products, as this will determine your production requirements. Additionally, processing certain powders—like whey proteins and flours—can present practical difficulties due to their tendency to bridge and resist flow.
Efficient sourcing, equipment selection, and scalable operations are essential to support sustainable business growth. We've compiled 5 key considerations to help you get started.
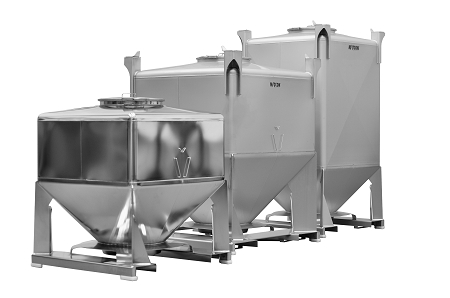
2.2 SCALABLE EQUIPMENT
Choosing the Right Equipment for Your Sports Nutrition Startup
Selecting equipment that can scale with your business.
Effective materials handling is central to successful sports nutrition manufacturing. Scaling up requires equipment that can handle powder flow issues, support different batch sizes, and maintain hygiene and quality to help you establish a reputation as a trustworthy manufacturer of sports nutrition products.
Choosing the right sourcing partners, setting up adaptable processes, and planning for future growth are essential for efficient, low-risk manufacturing. You should also assess whether continuous or manual processing best suits your production needs as your business scales.
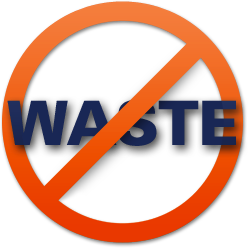
2.3 SUCCESSFUL SCALE UP
Minimise Waste When Scaling Up to Larger Volumes
Focus on each step of the manufacturing process and how ingredients move between them to keep production lean and efficient.
Lean manufacturing focuses on reducing waste to maximise profit, which is especially important for high-volume, low-cost sports nutrition production. Implementing Intermediate Bulk Containers (IBCs) helps minimise the common sources of waste by keeping ingredients contained, reducing cross-contamination, and allowing flexible, efficient processing across multiple recipes.
2.4 IDEAL FACTORY LAYOUT
The Ideal Sports Nutrition Factory Layout
Which manufacturing layout and blending process suits your needs?
This guide reviews three common factory layouts for sports nutrition manufacturing, outlining their setups, advantages, and disadvantages. It will help you choose the layout that best aligns with your production needs.
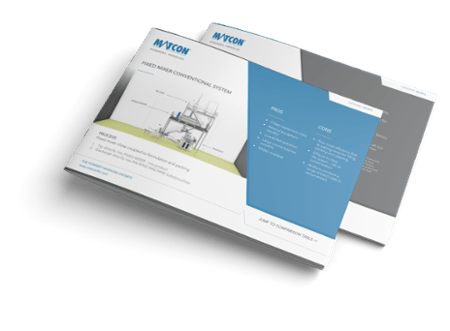
Staying Competitive in the Sports Nutrition Industry
To lead in the sports nutrition and functional foods market, manufacturers need to combine innovative product development with efficient, flexible production processes.
Your production must be agile to respond to evolving consumer preferences, ensure product safety and quality to protect your consumers and brand reputation, and have capacity to scale up. Embracing automation, improving supply chain agility, and maintaining compliance with regulatory standards can help manufacturers meet market demands and maintain a competitive edge.
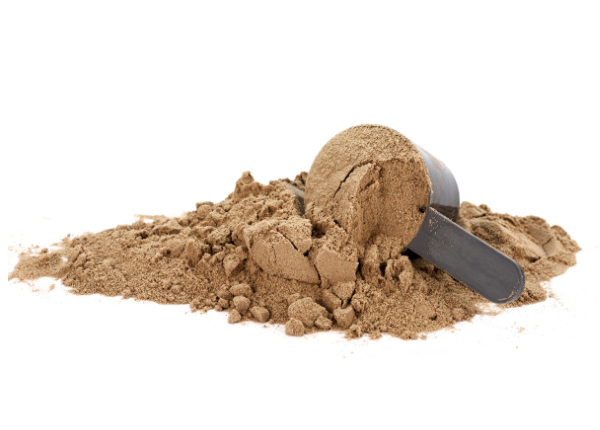
3.1 MAINTAINING HIGH PRODUCT QUALITY
Manufacturing Protein Powders
Managing sticky and poor-flowing powders while maintaining high product quality.
Efficient protein powder manufacturing requires careful attention to ingredient quality, powder handling, and production flexibility. Protein powders are notoriously sticky, resulting in the need to manage powder flow challenges, prevent cross-contamination, and support recipe changeovers to meet growing demand for personalised nutrition. Investing in adaptable powder handling systems and robust hygiene controls enables manufacturers to produce high-quality, tailored nutritional supplements and protein powders while maintaining operational efficiency.
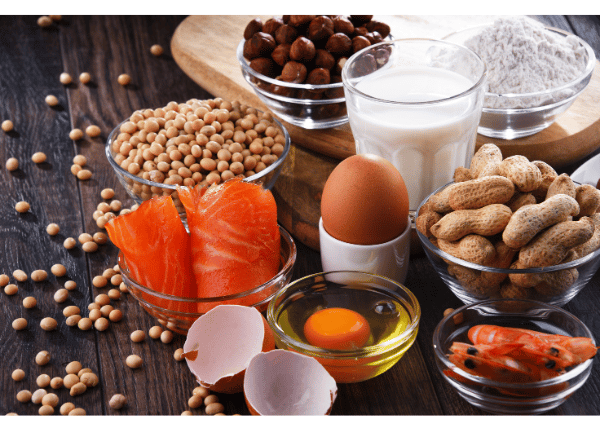
3.2 ALLERGEN HANDLING
Avoiding Allergen Cross-Contamination
Efficient and controlled allergen handling protects your consumers and your reputation.
Allergen cross-contamination can occur at multiple stages, including ingredient handling, production changeovers, equipment cleaning, and storage. Robust processes, such as utilizing closed systems, implementing thorough cleaning procedures, and maintaining proper segregation of ingredients are critical. Using scalable equipment and integrated powder handling systems improves allergen control, reduces cross-contamination risks, and helps meet industry regulations.
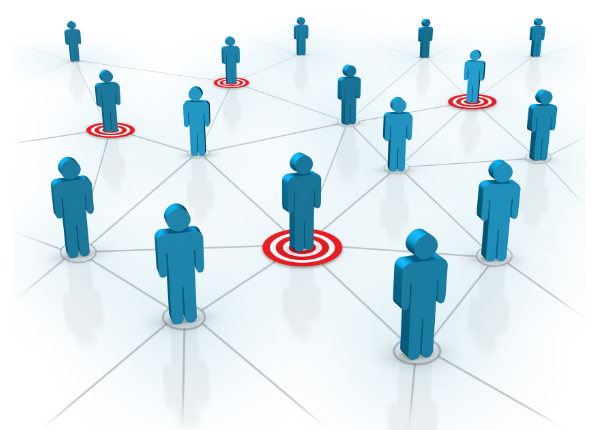
3.3 MEETING DEMAND
Meet Production Demand in the Sports Nutrition Industry
When mixing small batches of different recipes, you need equipment that can meet your needs.
Whilst some manufacturers in the nutrition and well-being industry focus on high volume production of single products, many sports nutrition manufacturers must deliver small batches of a variety of products, efficiently and in line with their finances.
As most producers now manufacture and deliver products covering everything from energy gels to protein powders, fast and effective changeovers are needed. Regular recipe changes and varied batch sizes can be large amounts of downtime whilst equipment is being cleaned and re-fitted, but those using a Matcon system can reduce waste and minimise downtime.
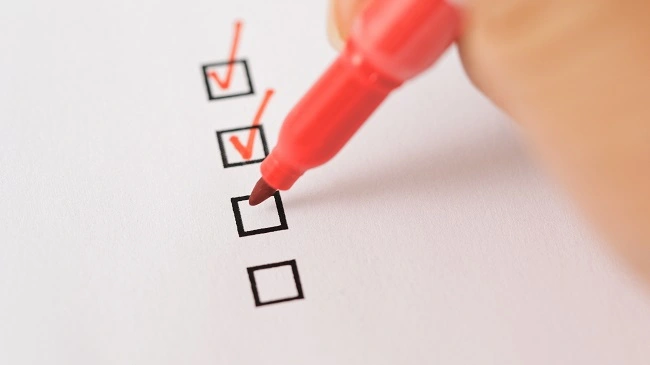
3.4 ACCREDITATIONS
Do Accreditations Help to Secure More Sales?
Having the relevant accreditation can not only demonstrate a high level of quality but also build confidence in your brand.
In a competitive marketplace such as the sports nutrition industry, brand reputation is everything. Once you have built a loyal customer base, you must do what you can to make the most of the opportunity. Having the right equipment will mean that you can consistently manufacture a high level of product, perform regular quality checks and create an environment that promotes excellence. High manufacturing standards make gaining accreditation easier, so it pays to know the best equipment for the job.
Calculate Your Return on Investment
Whether you are a start-up business or an established sports nutrition manufacturer, you need the most efficient equipment that guarantees a high return on investment.
Many of our customers want to become more efficient, running a leaner operation but maintaining a high-quality product. Whether you work in the sports nutrition industry, pharmaceuticals, food or even animal nutrition, your equipment must enable you to produce high-quality products in a cost-effective way.
To help you discover cost savings at the industrial mixing stage, we have developed an easy to use ROI Calculator.
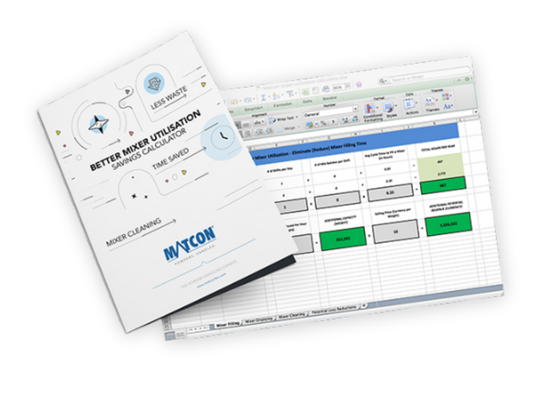
Quadro Mills for Sports Nutrition & Nutraceuticals
Quadro Engineering, another business unit of IDEX MPT, is the trusted provider of milling, screening and size reduction equipment. With 45+ years of experience, backed by pharmaceutical standards with food know-how, Quadro mills minimise product loss and improve efficiency.
Related Articles
Have look below at some of our related content to find out more.
Contact Our Team
Transform your manufacturing process.
The Original Cone Valve IBC Manufacturers
At the heart of the Matcon system you will find the Cone Valve - invented, patented and developed by us. We help manufacturers overcome issues of mix segregation, containment and bridging that are inherent in traditional powder handling systems. Discover our unique approach to powder handling and the innovation that underpins all that we do.
About us