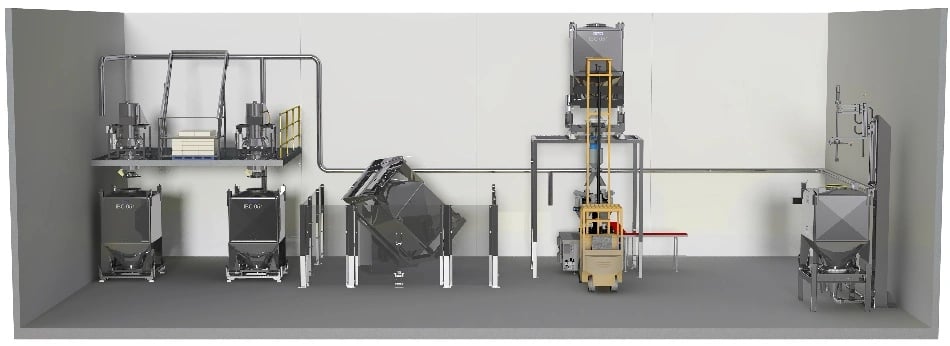
INDUSTRIES
Beverages & Powder Drink Mixes Manufacturing Equipment
Frequent recipe changes can result in high manufacturing costs and excessive inventory if not carefully managed.
MATERIALS HANDLING SYSTEMS
Powder beverages processing and blending equipment
Our hygienically designed powder handling and mixing system is all you need for the efficient production of powder-based beverages and drinks. By decoupling the processing steps we enable companies to achieve a flexible manufacturing system.
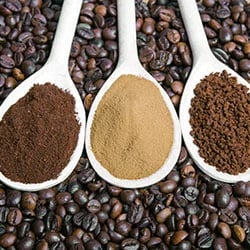
YOUR CHALLENGES
Mixing challenges for beverage & powder drink mixes manufacturers
With a growing appeal for more varied beverage and drink flavours as well as dietary trends including lactose-free and veganism, beverage manufacturers are having to change how they produce their products - from the processes they use to the industrial powder handling and mixing equipment they choose.
Increasingly large recipe portfolios mean many changeovers which significantly impacts production time.
Powder mix segregation is a risk, particularly with 3 in 1 coffee mixes, due to the different particle characteristics.
Problems with dust create cross-contamination risks.
HOW WE CAN HELP
Improve beverage & powder drink mixes manufacturers productivity
Matcon's bulk material processing IBC solutions are designed to optimize your production line to ultimately make it more flexible. By employing parallel processing, the manufacturing process steps (formulation, mixing, packing and cleaning) are decoupled, with each process step taking place independently.
The act of separating these manufacturing stages creates the potential for multiple processes to take place simultaneously, allowing manufacturers to produce more than one batch or different recipe batches at any given time, hence becoming more efficient.
Our unique Cone Valve Technology located within each IBC protects your blended powders against segregation during the discharge process, maintaining their integrity and quality.
With a Matcon IBC tumble blender, ingredients are fully contained within the IBC so there is no Blender to clean, making lengthy product changeovers a thing of the past.
The system remains closed at all times as all powders are contained within the IBC, eliminating any risk for cross-contamination and offering dust containment for a cleaner environment and operator safety.
OUR EXPERIENCE
Systems to meet the strictest of food safety requirements
Keeping dry ingredients contained is vital for beverage drink industry manufacturers that use 'free-flowing' powders.
Matcon has years of experience from working within the food, drink and beverage sector therefore we understand the importance of complying with strict food safety, hygiene and nutritional regulatory standards such as FDA Food Safety Modernisation Act (FSMA), Good Manufacturing Practices (GMP) and European Hygienic Engineering & Design Group (EHEDG).
We have supplied flexible and efficient production systems to numerous companies around the world making a wide variety of instant beverage mixes including 3 in 1 coffee, tea blends and powdered drink mixes. Our IBC systems have enabled our customers to increase productivity, reduce costs and improve product quality.
If you are mixing beverages for the sports nutrition industry, visit our page for sports supplement manufacturers.
OUR APPROACH
Working with beverage & powder drink mix manufacturers
We deliver a wide range of IBC powder handling systems and blending equipment, from the simple start-up to the more complex automated, multi-mixer, multiple packing line configurations.
Central to our IBC technology is the Cone Valve, offering automatic and controlled discharge of virtually any powder type. Cohesive materials are stimulated to flow, whilst free-flowing powders are controlled. Our Cone Valve has continually proven to overcome the traditional powder handling issues of bridging, rat-holing, segregation and degradation.
With an IBC Blending System, your recipe batch is mixed directly within the IBC with no product in contact with the Blender itself, making product changeovers virtually instantaneous. And with the added benefit of the IBC Blender being able to accommodate different container sizes according to your batch size, your manufacturing flexibility and efficiency is instantly improved.
Our scalable modular design is perfect to expand upon as you innovate and grow your product portfolios and increase throughput to develop your business.
SYSTEM MODULES
Powder Handling Systems for Beverage Manufacturers
This simple system is all you need to get started the right way. By decoupling the processing steps we enable companies to achieve a flexible manufacturing system.
The Matcon system is based on using Intermediate Bulk Containers (IBCs) to transport powders between manufacturing steps and as a blending vessel. Because everything is contained within the IBC, there is no clean-down of the blender between recipe changes, which gives you the ultimate flexibility of operation.
LEARN MORE
Resources and Information
Equipment guidance and useful information for manufacturers of beverage mixes and powder based drinks.
- 5 Ways to Future-proof Your Food and Beverage Production
- Beverage Manufacturers Increase ROI With IBC Blending
- Case Study: Wetra Coffee 3-1 Coffee Mixes Manufacturer
- Case Study: Boh Tea - Beverages
- Case Study: Multitech Foods
- Resolving Ratholing for Beverage Powders
- How to Prevent Bridging and Arching Problems
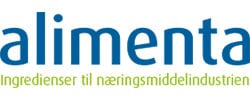
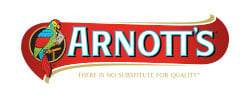
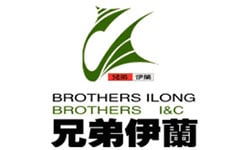
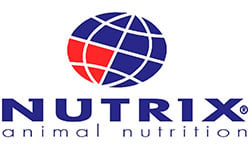
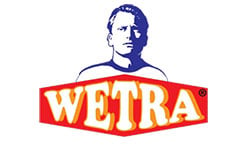
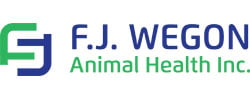

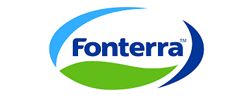
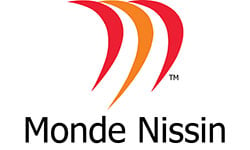
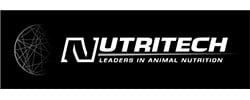
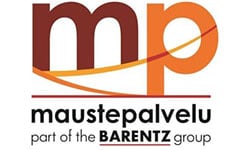
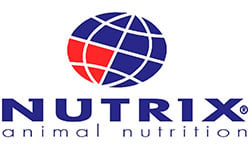