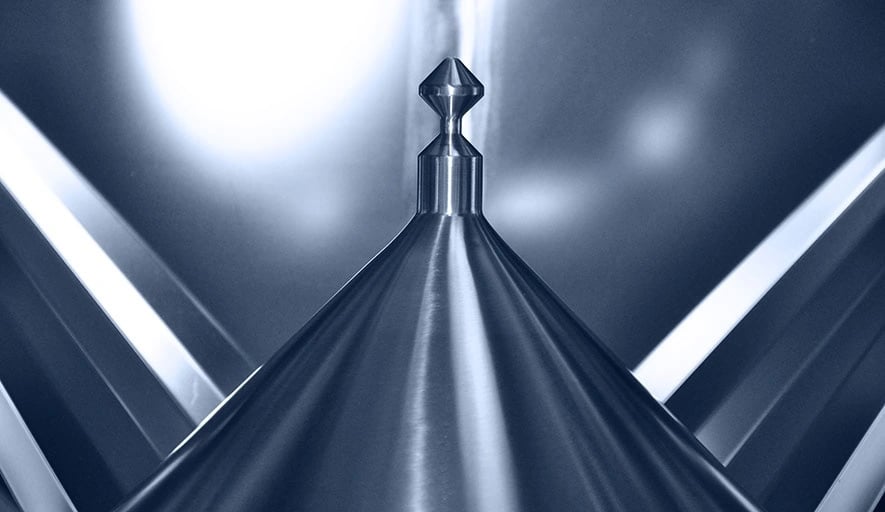
CONTAINED, CONTROLLED POWDER FLOW
Valves for Powder Discharge
Matcon manufacture a range of unique valves, designed to control the discharge flow of powders and overcome the challenges of bridging, ratholing and mix segregation.
At the heart of our offering is the original Matcon Cone Valve Technology which has stood the test of time and continues to offer undisputed benefit to our customers.
As the original manufacturer of Cone Valve Technology we have decades of designing solutions across a wide range of applications and helping our customers transform their powder handling processes.