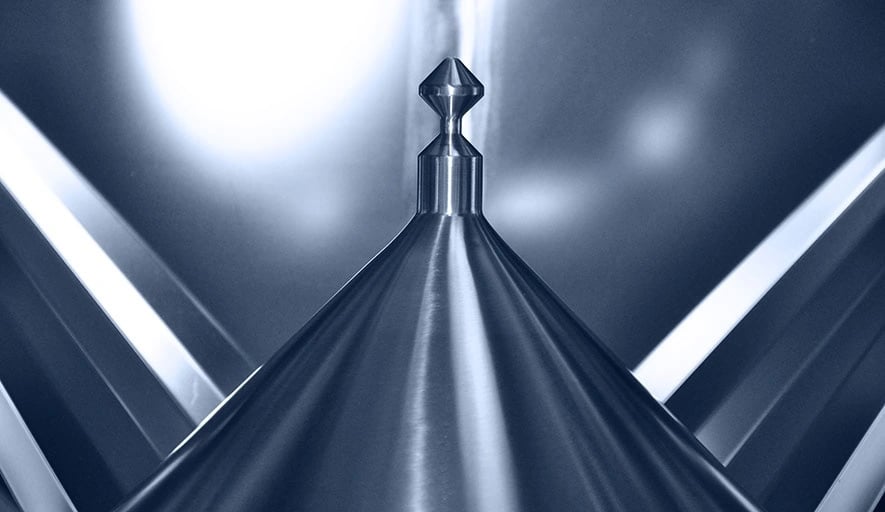
PRECISE, CLEAN, FAST
Powder Recipe Formulation
Speed up recipe formulation & improve throughputs.
Recipes are formulated offline directly into Intermediate Bulk Containers (IBCs) and brought into the manufacturing process flow as needed.
Check weighing & material tracking provide reliable batch traceability.
Powder Handling System Modules
Matcon's formulation modules are just one element of the efficient powder handling systems we offer. Our processing equipment helps you at every stage of your powder handling process, streamlining your operations, improving product quality and helping increase your margins. By decoupling the manufacturing steps, we enable manufacturers to achieve a flexible and efficient powder handling system.