BATTERY
Key Facts for Owners and Managing Directors
From initial concept to final installation and commissioning, our experienced team will deliver a LEAN, scalable solution with high OEE rates and in line with SMED.
Expandable, robust and easy to maintain – a Matcon system will deliver a favourable return on your investment in the long term.
Get the Matcon Advantage
Battery technology is always evolving and changing. Every day, new materials and processes are investigated to see if they can help lower costs, increase efficiency, and satisfy rising demand. Matcon has the experience and expertise to be able to offer you the best possible solutions for manufacturing with flexibility and scalability in mind.
We understand the lithium-ion battery industry, and how every type of battery needs different production conditions. We also understand how important it is to provide the right climate, control and containment for each process stage.
Related Pages
Select your area of responsibility for specific information tailored to your area of expertise.
Potential Efficiencies
- Cone Valve technology protects the homogenous blend and controls difficult to handle powders.
- Decoupling processes allows individual equipment OEE rates to be significantly improved.
- Automation reduces operator costs & operator exposure to hazardous material and lessens the risk of human error.
Impact on Unit Profitability
- A compact system reduces the need for factory space.
- Cone Valve IBCs reduce waste in the system and improve cash utilisation.
- The ability to make to order reduces the need for WIP or Inventory, saving on stock levels & warehousing space.
Typical ROI
- By cutting waste at all levels the cost/kg of the final finished product is significantly improved.
- Reduced cleaning times from 480 hours to 70 man hours have been achieved.
- Inventory can be eliminated which then releases cash in the business.
- Labour costs have been significantly reduced by virtue of system automation and lesser cleaning burdens.
- 55% reduction in Manufacturing time with better mixing efficiencies.
- A modular system design allows for easy expansion as the business grows, simply add on more modules to meet the production demands.
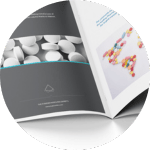
Case Studies
Read on to discover how we help companies around the world create flexible, agile manufacturing plants.
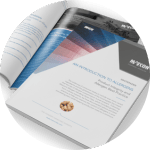
White Papers
Understand more about how to get the best from your powder handling site with our resources.
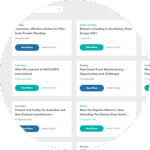
Blog
Read more about powder handling solutions, technical advice and industry insights from the experts.
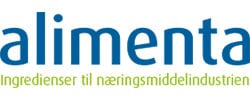
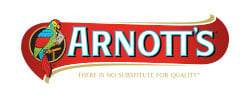
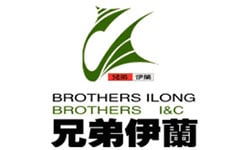
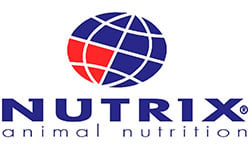
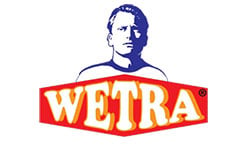
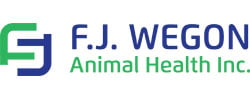

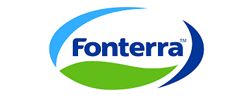
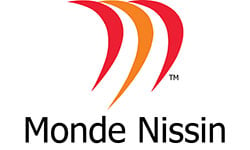
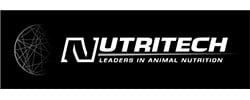
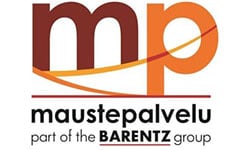
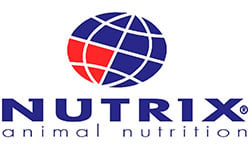
CONTACT US
Request a Free Site Appraisal
Our Sales Engineers have a wealth of experience in helping companies to design and specify the right solution to fit your business, regardless of capacity demands.
If you would appreciate a visit please submit the form below: