Powder Segregation Due to Elutriation
Is the discharge process causing your product to segregate?
Air displacement through powders with varied particle sizes can cause segregation, leading to an inconsistent end product.
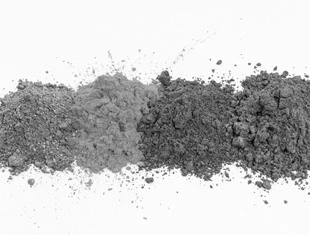
Why is My Product Segregating?
The value added at blending can be wasted if your powders don't discharge correctly.
Having spent time and therefore money creating a perfectly mixed recipe it is frustrating to be seeing poor product quality further down the production line.
This will be due to the various powder particles having separated somewhere along the process. One common cause is when the particles are separated during free fall due to air resistance. As the particles settle your resulting product is often segregated.
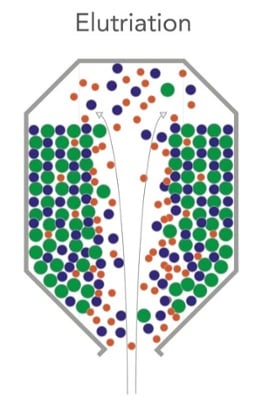
What are the Common Causes of Elutriation?
With modern recipes using a range of powder types this can be a risk.
Elutriation occurs as the air circulates back up into the container when product is discharged. This displaced air carries the finer particles back up through the container, thereby segregating the mix. This is particularly common with particles under 50µm whereby if the upward velocity of the air exceeds the terminal free-fall velocity of the fines, they remain in suspension as the larger particles continue to move downwards.
Materials that are displaced will fall inconsistently back into the container or hopper segregating the mix. This is a common problem when emptying a fixed mixer or emptying a butterfly valve or slide valve container into the downstream process equipment.
How to Stop Your Powders From Segregating
Is the discharge process causing your powders to segregate?
The Matcon Cone Valve technology within each IBC removes this risk of elutriation because the volume of vented air is kept to a minimum. The annular gap created as the cone lifts controls the flow of air back into the IBC as the height and speed of the lift can be graduated to maintain control of the incoming air.
Furthermore Matcon have developed a hygienic anti-vacuum vent to help maintain an equal pressure system when discharging material.
Learn more about the Matcon Cone Valve with the video opposite.
CONTACT US
Did we answer your powder handling problem?
If you didn't find the answer you were looking for, complete the form below and one of our powder handling experts will help you diagnose and solve the issue.
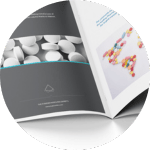
Case Studies
Read on to discover how we help companies around the world create flexible, agile manufacturing plants.
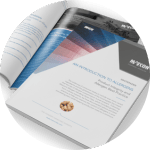
White Papers
Understand more about how to get the best from your powder handling site with our resources.
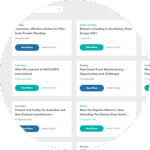
Blog
Read more about powder handling solutions, technical advice and industry insights from the experts.
Companies We Work With
Learn about the companies currently using Matcon Systems to optimise their production efficiency and profitability.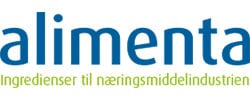
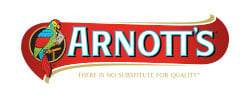
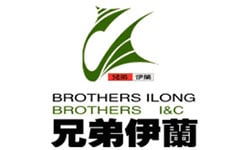
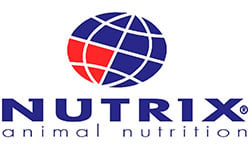
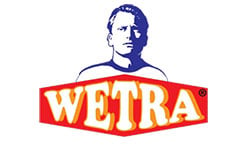
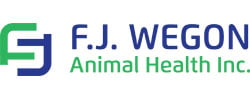

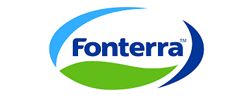
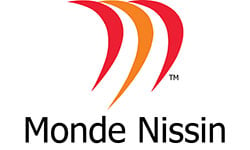
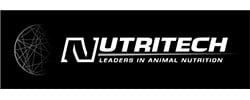
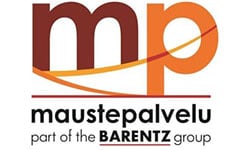
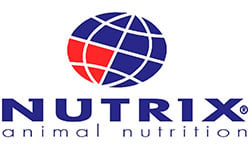