Powder Mix Segregation
How to Prevent Powder Segregation?
If you are experiencing issues with poor product quality, it is probably due to the fact that your powders are segregating somewhere in your manufacturing process.
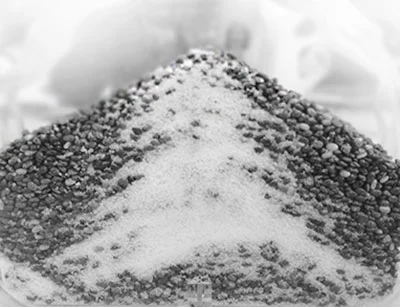
Is my product segregating?
Even the best quality mixture can be undone by improper powder and material handling along the manufacturing process chain.
When you are moving, pouring, conveying or processing materials, each step can affect product quality. The product can become un-mixed so that there is no longer the same proportion of ingredients in each of the consumer consumption units (or ‘doses’ to put it another way).
In some market sectors this may not matter too much, for example you could sometimes tolerate occasionally getting a drink that is a bit too sugary or not flavored enough. But for some products that contain vitamins & minerals it is vital that the correct amount reaches the consumer – in this instance there is no doubt the importance of avoiding the breakdown of an homogeneous mixture.
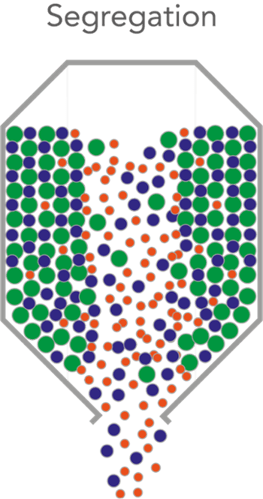
What are the Common Causes of Powder Segregation?
With recipes that use multiple powder material segregation can be an issue.
In order to provide high quality, high functioning products, modern recipes often use a variety of different powder types, all of which have different particulate characteristics. Separation of a mixture is caused by the differences in size, shape or density of the powder particles.
Particle size is probably the most significant source of segregation. When transferring product between processing steps, the in-flight material will travel at different velocities depending on particle size, this creates what is known as trajectory segregation. Larger particles will be projected further, leaving the smaller ones behind.
A further cause of segregation is percolation. The small particles move downwards through the mass falling into the spaces between the larger particles. It occurs during shaking, or vibration of the hopper when charging or discharging its contents. At the same time, the larger particles move upwards in the so called ‘Brazil Nut effect’ as voids are created then filled in with the smaller particles forcing the larger particles upwards. These changes in powder state often occur unknowingly through traditional handling methods.
How to Stop Your Powders from Segregating
Is the discharge process causing your powders to segregate?
Matcon IBCs are designed to create mass-flow of powders due to their 60° hopper angle, smooth interior surfaces and unique Cone Valve technology. Mass-flow is defined as all the powder is in motion across the whole of the container whenever any is withdrawn. It produces a first in-first out flow sequence, eliminating any stagnant areas, and providing a steady discharge with consistent bulk density, and a flow that is uniform and well-controlled.
This keeps the mix homogeneous during the discharge process and helps to maintain product quality.
Discover the Cone Valve with this helpful video.
CONTACT US
Looking for the Next Step to Resolve Powder Segregation?
Complete the form below and one of our powder handling experts will help you prevent powder segregation in your process.
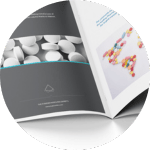
Case Studies
Read on to discover how we help companies around the world create flexible, agile manufacturing plants.
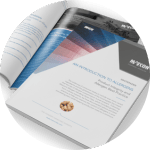
White Papers
Understand more about how to get the best from your powder handling site with our resources.
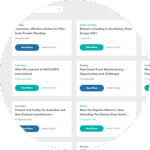
Blog
Read more about powder handling solutions, technical advice and industry insights from the experts.