When developing a new design of pharmaceutical manufacturing plant for oral solid dosage (OSD) products, the way in which you design your production lines can dramatically influence the productivity and efficiency of your business. We discuss the three main options for materials handling during production, and consider the benefits and drawbacks of each.
Efficient Materials Handling
It is, of course, vital to know what steps are involved in making an OSD product to generate consistently uniform, high quality batches. What ingredients are needed, in what quantities and proportions? What processes are involved and what equipment is required?
But an often-overlooked element is how you move materials between the steps of a given production line. Paying careful attention to materials handling is important so as not to waste time, effort, or money. Idealistically at the early stages of developing a new design of pharmaceutical manufacturing plant. The three main types of materials handling each have their own benefits and drawbacks.
Continuous processing
In this system, the equipment required for one stage of the process is directly coupled to that required for the next. In continuous tablet manufacture, for example, ingredients are fed into a mixer, blended ingredients are dispensed directly into the tablet press, and pressed tablets are fed straight to coating and onwards to the packing line.
This type of system effectively removes the need for materials handling at all. Since materials are kept within one pipeline, spills, dust and contamination are minimized, and little effort is wasted transporting materials from process to process.
However, in practice, it is difficult to establish a completely continuous process, and some steps are inevitably quicker than others. This means the entire production line is only capable of operating at the pace of the slowest step.
Also, should a fault occur, that entire production line must be closed to mend the broken part or remove and clean the blockage, and if contamination should occur, the entire batch must be discarded and wasted.
Another drawback is the inflexibility of a continuous system. Say a customer placed double their usual order: it would take twice as long to manufacture. It is not straightforward to modify a continuous process in order increase the capacity, or change the recipe, for example.
Manual processing
Manual materials handling is arguably the simplest, and is achieved by using cheap-to-purchase boxes, tubs or drums to physically move ingredients and products around the facility.
This approach is very flexible. By uncoupling the steps from each other, each process can operate at its optimal speed, and the outputs of a process can also be fed into more than one pipeline, so it is easier to operate parallel production lines than a continuous system.
Manual handling, however, is wasteful. Moving drums of ingredients by hand is slow, consumes effort, incurs health and safety risks, and limits production capacity. It is much more inefficient than automated processes.
With manual handling, it can also be difficult to track inventory and monitor batch quality. Each container of a sub-lot of a batch must be individually tracked, and results in crowded production areas. As the number of sub-lots increases the risk of error escalates.
Intermediate Bulk Containers (IBCs)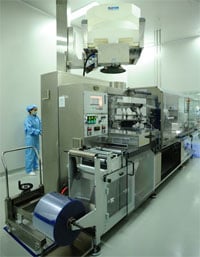
With IBCs, while processes are disconnected from each other, so they operate autonomously. With a well-designed IBC system material loss or contamination is reduced, and less cleaning is required. The system is flexible enough to operate parallel processes, and since individual steps can operate at their optimal rates, productivity is improved. The bigger volumes of powders and tablets afforded by using IBCs means there are fewer container movements and less make/break connections and less tracking to be performed.
Conclusion
While manual materials handling is cheap and simple, and continuous processing eliminates contamination risks, using an IBC powder handling system provides the best of both worlds, while also eliminating many of the inefficiencies of either of these traditional materials handling options.
Posted by
Matt BaumberTopics:
Pharmaceutical