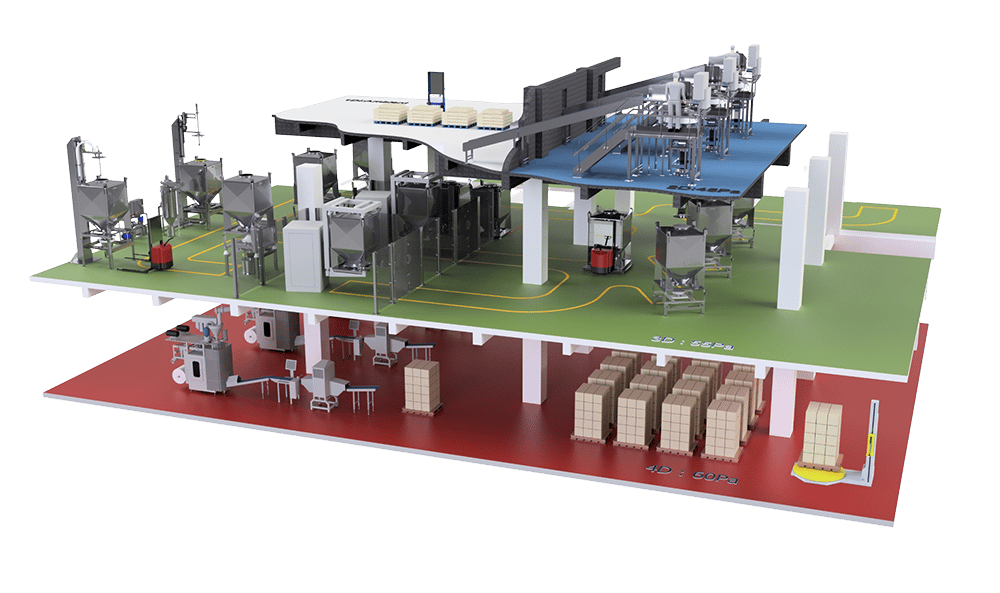
Optimising Efficiency and Production Throughput
Advanced Material Handling Solutions for Battery Manufacturers
WHY MATCON
Enhancing Battery Efficiency through Expert Powder Management
At Matcon, we understand how critical powder quality is to the performance of battery components like anodes and cathodes. Our technology is designed to ensure consistent and pure powders, providing a reliable foundation for meeting the demands of modern production.
A Legacy of Innovation
With a heritage of over 40 years, Matcon has invested in refining our expertise in powder handling to support the advancement of battery technology. We have a track record of success in collaborating with industry leaders and innovators, and our solutions are designed to meet the evolving needs of this rapidly changing field.
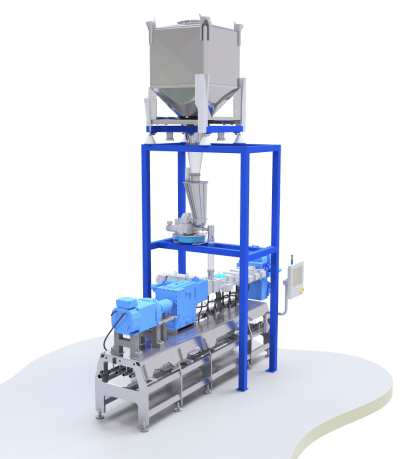
In Collaboration with Industry Experts
Matcon proudly works with forward-thinking corporations and institutions, including:
- Battery start-ups who are at the cutting edge, seeking innovative solutions dedicated to efficient production and strategic planning.
- Academic and research entities who prioritise developing new battery chemistries and champion the shift towards sustainable, practical battery technologies.
- Established battery technology leaders who balance innovation with the risk entailed in delivering competitive, giga-factory projects.
ENVIRONMENTAL RESPONSIBILITY
Battery Recycling – Closing the Loop
With the ability to consolidate multiple FIBCs or sacks of black mass into a single, compact system, IBCs offer flexible storage and transport options that adapt to facilities of all sizes. Their scalability helps accommodate a range of operational capacities, making them suitable for many recycling setups.
Matcon’s automation solutions ensure consistent and precise dosing while reducing manual intervention. This approach improves safety, controls operational costs, and delivers reliable, repeatable processes—helping facilities achieve efficient recycling outcomes.
For the Visionaries and Innovators
Emerging into the Future of Batteries
For industry professionals seeking efficient production and innovative solutions, having a partner that understands and scales with your growth is essential. Matcon offers scalable solutions that can adapt to address the complexities of your battery chemistry powders and production challenges. Our systems not only help you achieve your goals but also ensure repeatable results, maintaining investor confidence.
For Gigafactory
Managers
Developing and Expanding Production Facilities
Matcon is working on some of the largest gigafactories, providing efficient powder-handling solutions that ensure high-quality output while keeping up with increasing demand. Our bespoke systems are designed for seamless integration into the current production processes, providing a smooth transition to increased capacity and productivity.
For the Scientists Turning Theory into Practice
Pioneering Battery Research
The quest to discover new chemistries and sustainable practices is reflected in Matcon's dedication to supporting the shift from lab research to large-scale production. In response to the growing R&D needs and the pursuit of higher ROI, we have delivered solutions mirroring our full-scale system's parameters. This integration encourages a space where experimentation and scalability combine with effectiveness.
OUR COMPREHENSIVE RANGE
Equipment for battery production
We champion the design and implementation of modular systems centred on Intermediate Bulk Containers (IBCs) for the efficient transfer and processing of powders. This modular approach affords flexibility, enabling integration of production steps, including filling, blending, feeding to downstream processes, packing, and cleaning. These systems are not only scalable but also ensure that cross-contamination is minimised, maintaining the integrity of your materials throughout the production cycle.
IBCs improve battery manufacturing by enabling fast changeovers, flexible processes, and less downtime. This boosts efficiency and helps manufacturers stay competitive. Matcon supports clients, from startups to gigafactories, in optimising production and meeting industry demands.
Discharge
Matcon's discharging systems enhance process efficiency through our innovative Cone Valve technology, which prevents bridging and segregation, facilitating mass flow. Additionally, they can handle powders heated up to 200 degrees Celsius.
Request a Consultation
Looking to improve your battery production process?
We specialise in enhancing powder handling systems for battery manufacturing. Our expertise allows us to analyse powder behaviour in detail and develop practical solutions tailored to your needs. To help you find the right approach, we offer complimentary powder tests wherever possible, demonstrating the effectiveness of our methods.
More than just a supplier, we’re here to be your strategic partner—working with you from initial testing to full-scale production. Let’s start the conversation and find the best solution for your production challenges.
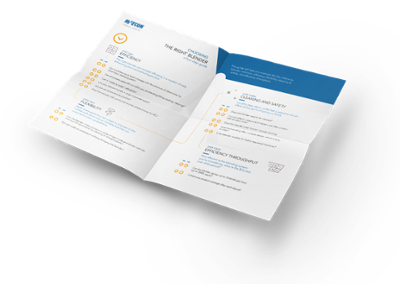
RESOURCES
Battery Developer Hub
Explore the Battery Developer Hub, your premier resource for gaining engineering insights into optimising powder handling in battery production. This dedicated resource offers insightful webcasts and expert engineering solutions. Discover more about our innovative equipment designed to address industry challenges and improve production efficiency. Engineer a better tomorrow, today!
Knowledge Hub
Manufacturing and handling powders presents a variety of technical challenges. Browse our Knowledge Hub for further technical insights and advice. All our resources are free to download and are created from decades of powder handling experience and expertise.
IBC Solutions
Learn about our solutions for handling the complex ingredients used in Lithium-ion battery production.
Our material handling experts can help
Speak to our team
Every breakthrough starts with a conversation. Our battery specialists are here to offer a fresh perspective and help uncover smarter solutions for your manufacturing challenges. Reach out today—sometimes, all it takes is a simple discussion to spark the transformation you need.
The Original Cone Valve IBC Manufacturers
At the heart of the Matcon system you will find the Cone Valve - invented, patented and developed by us. We help manufacturers overcome issues of mix segregation, containment and bridging that are inherent in traditional powder handling systems. Discover our unique approach to powder handling and the innovation that underpins all that we do.
About us